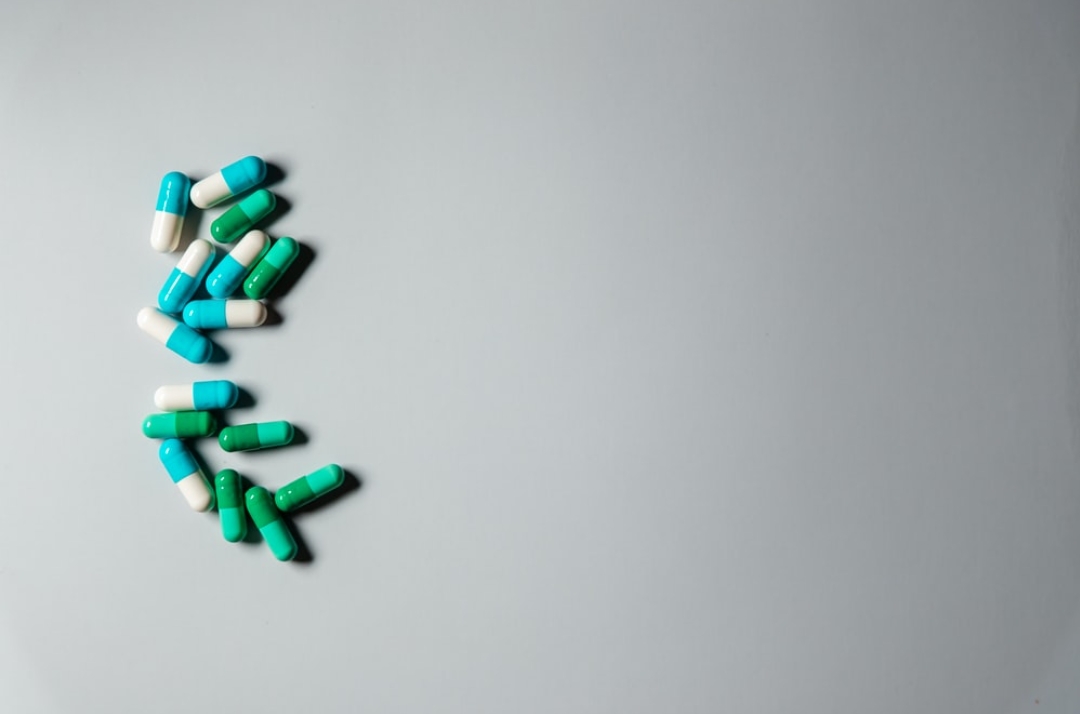
Procedures for product recall in pharmaceutical industry
Recall is the act of officially summoning someone or something back to its place of origin. A product recall is defined as a request to return, exchange, or replace a product after a manufacturer or consumer watch group discovers defects that could hinder performance, harm consumers, or produce legal issues for the producers.
Due to a greater awareness of consumer safety concerns, many companies focus on taking preventive measures, using an internal product recall team, and implementing quality control procedures designed to reduce the risk of—and perhaps even prevent—major product recall expenditures.
RISKS OF A PRODUCT RECALL
To reduce and contain risk, the product teams should document all recall actions, including customer, distributor, user, and public communications
If suppliers or component manufacturers are responsible for the recall, it is important to reach out to them as soon as possible to understand the reason for the recall, scope of the recall, and how they plan to address it.
Track all recall-related costs to facilitate future insurance claims and claims against responsible suppliers and component manufacturers.
In conjunction with government regulators, send follow-up recall notices to customers, distributors, and users—making sure to keep copies of those notices. Post a notice on your organization’s website and prepare a notice for retailers to post on their sites, as appropriate.
When affected by a recall, it can be beneficial to work with corporate communications or public relations to ensure the proper messaging reaches the correct audiences. In addition, working with legal counsel can help your organization understand its full legal risk and take appropriate course of action.
While not desired, a product recall should be seen by an organization and its employees as a potentially positive opportunity to eliminate or reduce personal injury, property damage, and harm to the reputation of the company and its products. In addition, it may help rebuild public trust in the organization and its products.
PREVENTION PLANNING FOR A PRODUCT RECALL
An organization-wide culture of product safety—including product management (manufacturing and sales), design, quality, use and testing, and literature—is the best means of preventing a product recall.
However, even with an established culture of quality, organizations face product recall risks due to human error, systems failures, and product or component failures. This is why it is important to have a documented response process if one or more of these errors occur and necessitate a product recall.
Having a response plan will help ensure the faulty products affect as few persons or organizations as possible, and will also help reduce the difficulty and expense associated with product recalls.
Procedures should be created that will permit tracking of all products sold, either by lot number or production period. Manufacturers should also consider using product registration cards for consumers to fill out and return, identifying information such as model number, style number, and special features of the product that was purchased. Registration cards, coupled with an easily retrievable customer database, can be an effective tool for identifying owners of recalled products.
The use of accurate records and product labeling can help manufacturers isolate defective products and potentially limit the scope of a recall. In addition, it can facilitate rapid and widespread notice to customers, distributors, and end users when a recall is needed.
PRODUCT RECALL TEAM APPROACH
The objective is to combine the team’s skills and experience to implement and periodically review product safety evaluation procedures, product recall plans, and product safety concerns raised internally or by user or governmental inquiries and complaints. It is important that people with the necessary requisite skill and product and marketing savvy are named to the product recall team and actively participate in its deliberations and testing. If the manufacturer does not have adequate or available internal resources, it may consider retaining outside expertise.
Ideally, the team will meet regularly to review public and internal information on safety issues, including items or procedures identified as toxic or hazardous by safety or industry organizations, governmental agencies, or consumer groups.
The team may want to develop internal operating and quality control procedures, such as component certification, product inspection during and after the manufacturing process, and product testing, including testing by an independent testing laboratory. Doing so will help ensure compliance with the Consumer Product Safety Improvement Act (CPSIA), which is enforced by the Consumer Product Safety Commission (CPSC).
RESPONDING TO A PRODUCT RECALL
A product recall is often seen as a process, one that is approached methodically and thoughtfully, with disciplined brainstorming, vetting, testing, and double-checking. Manufacturers may wish to carefully and systematically investigate and analyze all product incidents. If an investigation indicates a product fails to comply with standards or creates a substantial risk of injury, then a formal report to the CPSC or other governmental agency may be required. Manufacturers may also want to act promptly to correct any inaccurate public reports or misperceptions contained in the CPSC’s product database or the media.
To avoid and minimize potential litigation or governmental exposure, the best antidote is prompt, clear, and concise notice to all persons affected by the recall, including direct notice to end users or consumers whenever possible.
For example, Williams-Sonoma Inc. was commended by the CPSC in 2001 for using its own electronic credit card records, in conjunction with bank credit card companies, to identify purchasers of recalled portable gas grills. By notifying purchasers individually and offering a full refund and $50 gift certificate, the company was able to make its recall successful, with more than 99% of the grills returned.
It may also be a good idea to explore product recall insurance to cover out-of-pocket costs associated with a recall.
Certain markets, such as children’s products, require additional steps in the event of a recall. The Consumer Product Safety Improvement Act (CPSIA) amended the Consumer Product Safety Act (CPSA) with significant new regulatory and enforcement tools. The CPSIA included provisions addressing lead, phthalates, toy safety, durable infant or toddler products, third-party testing and certification, tracking labels, imports, ATVs, civil and criminal penalties, and SaferProducts.gov, a online consumer database to track unsafe products.
Visit DocMode for Courses and lectures